Get a Quote For Your Next Home Project
Renovation Vs Remodel: What’s The Difference?
Renovating and remodeling are two of the most common terms used when it comes to home improvement and construction projects. While they are often used interchangeably, they are actually two different processes. Teakwood Enterprises in Fredericksburg, VA is here to explain the difference. Learn more down below and let us help you with your next…
Read MoreTips for Building an Eco-Friendly Custom Home
Building an eco-friendly home is a great way to reduce your environmental impact and save money in the long run. It may seem like a daunting task and homeowners might not know where to start. Luckily, Teakwood Enterprises Inc., in Fredericksburg, Virginia, wants to help homeowners create custom green homes that are as efficient and…
Read MoreCost Considerations When Building a Custom Home
Building a custom home can be an exciting and rewarding experience, but the process can be expensive. Before homeowners start building a house, Teakwood Enterprises Inc. wants everyone to understand the costs involved. A custom home design can take several months to complete and we want to make sure homeowners are prepared. Read on and…
Read MorePopular Design Trends for Custom Homes
Designing a custom home can be a fun and exciting process. Not only do you get to create a space that is totally unique to you, but you also get to consider the latest trends in home design. Teakwood Enterprises Inc. wants to help inspire your custom home design. Here are some of the most…
Read MoreNavigating the Design Process: Tips for Creating Your Dream Custom Home
Building a custom home is an exciting and rewarding process, but it can also be overwhelming, especially when it comes to the design phase. With so many options and decisions to make, it’s easy to get lost in the details. However, with a little bit of planning and organization, you can make the process much…
Read MoreWorking with a Custom Home Builder: How to Communicate Your Vision Effectively
When building a custom home, one of the most important aspects of the process is effective communication with your home builder. The builder plays a vital role in bringing your vision to life, and clear communication is essential to ensure that the final product meets your expectations. Here are some tips for communicating effectively with…
Read More4 Home Remodel Projects That Offer The Best ROI
If you’re looking for home remodeling projects that offer the best return on investment (ROI), you’ve come to the right place. As Fredericksburg’s premier custom home builder, we specialize in helping homeowners just like you enhance the value of their current homes with our award-winning remodeling services. Today, we’ll explore four of our most popular…
Read MoreIs Building a Custom Home Right For You?
Are you tired of living in a home that doesn’t quite fit your lifestyle? Are you cramped in a small space and constantly running out of room? Or maybe you’re just sick of the hassle of moving every few years. If any of these sounds like you, it may be time to consider building a…
Read More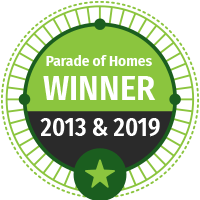

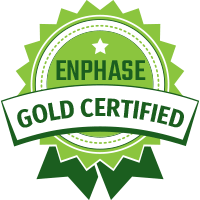
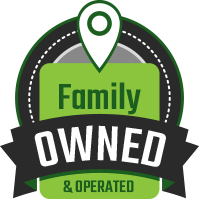
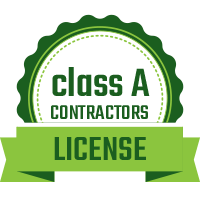
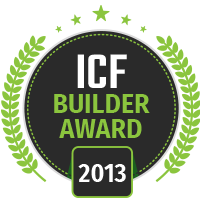

3351 Shannon Park Dr, Fredericksburg, VA, 22408
Email Us!
Office Hours
M-F: 9am – 5pm
S-S: By Appointment Only